Driving High Current With Tmr Magnetic Sensors
Within an embedded system, a magnetic sensor’s role is to detect the presence and/or motion of a magnetic object and signal the microprocessor to execute a desired action. Some engineers would prefer to control a load directly with a magnetic sensor – e.g., to switch ON/OFF relay coils, battery power, or an LED. Magnetic sensors can typically sinkcurrents of up to 20mA, which can be a limitation in cases where higher currents need to be switched ON and OFF.In these types of cases, it is best to couple the sensor with a discrete power MOSFET that can withstand the required current.
Advanced RedRock® magnetic sensors are based on TMR (Tunneling Magnetoresistance) technology. Providing Ultra-low power consumption and a small footprint, these sensors are ideal for use with battery operated systems.These tiny sensors can also be made to switch higher current loads ON/OFF as one can control a discrete power MOSFET directly via the sensor’s output pin. Application examples might be a small motor or a strip of LED diodes.
A MOSFET is a voltage-controlled device. The gate bias voltage controls the conduction between the source and the drain. The leakage current of the gate-oxide is relatively mall, which makes it ideal for battery-operated systems as compared to using a bipolar junction transistor. TMR sensors are active LOW devices. When a magnet is present, the output goes LOW. Conversely, when no magnet is present,the output goes HIGH. By connecting this output to the MOSFET’s gate, the MOSFET can be turned ON/OFF, allowing current to flow or to cut the current flow completely.
Normally-ON Operation: In Fig. 1a, a P-channel MOSFET is used to perform an ON status control. In a normally-opendesign, (Fig. 1a) a sensor’s output is HIGH when no magnetic field is present and the P-channel MOSFET (Q1) won’t turn ON; therefore, there is no current flow through RLOAD. When a magnet approaches and provides sufficient magnetic flux density to the RR12x, the sensor’s output will go LOW so the Vgs of Q1 will be low enough to turn ON the source-drain channel. Therefore, there is a current flow through RLOAD.
Normally-OFF Operation: In Fig. 1b, the N-channel MOSFET is used to perform the OFF status control – and will have the opposite behavior of a P-channel MOSFET. As shown in Fig. 1b, there is a continuous current flowing through RLOAD when the sensor’s output remains HIGH (with no magnetic field present).
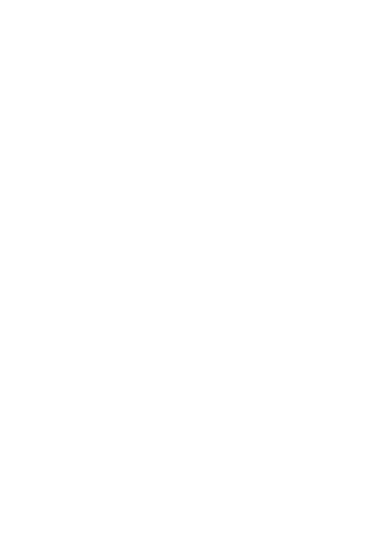
Additional Gate Components: The gate-oxide of the MOSFET is a thin film layer – measurable in nanometers –therefore it is very sensitive to electrostatic discharge (ESD). In order to protect the MOSFET (Q1), two zener diodes (D1& D2) are connected to the gate of the MOSFET to provide ESD protection. Additionally, the gate of the MOSFET can be considered to be a small capacitor. During high-frequency ON/OFF operation, the inrush current charging the gate of the MOSFET could damage the device. A resistor (R1) is connected to the sensor’s output pin and the gate of the MOSFET to limit the inrush current level. The typical value ofR1 can be from 100 ohms to 10K ohms. A higher value of R1may cause a slow rise time in high-frequency operation.
Protecting the MOSFET When Driving Inductive Loads: When driving a small relay or other inductive load with a discrete MOSFET, some protection is required in order to prevent transistor breakdown. When an inductive load, such as a coil, is switched OFF, back-EMF will be generated from the coil and this surge voltage will be applied to the transistor (Q1). A fly-back/flywheel diode (D3), shown in Fig. 2, can help to send energy back to the power source. While a general-purpose diode with adequate reverse breakdown voltage is sufficient, a Schottky diode with its faster response is sometimes used for this purpose.
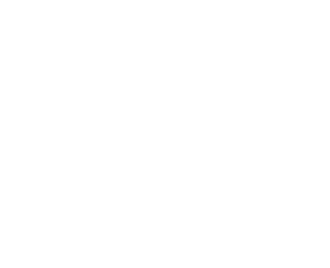
A PhotoMOS Relay as alternative to a MOSFET Transistor: A photo-isolated MOSFET relay is an alternative option to drive high current and can be controlled directly by a RedRock® sensor. The structure of the MOSFET relay consists of two isolated separate sides – the input side and the output side. The input side is an LED diode and the output side contains photodiode arrays & MOSFETs as shown in Fig. 3. When forward current flows through the LED, it starts to illuminate. The photodiode arrays on the output side will turn ON to control the conductance of the MOSFET.MOSFET relays offer many advantages over traditional electromechanical relays such as smaller footprint and more reliability.
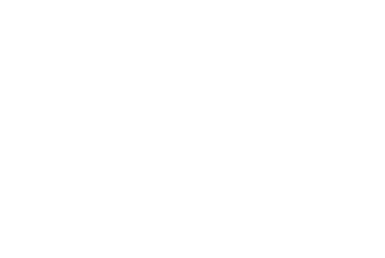
In addition to RedRock® TMR magnetic sensors, Coto Technology offers a high performance MOSFET relay, trademarked CotoMOSTM. Coto Technology’s CotoMOSTM andRedRock® TMR sensors can work together to provide magnetically-controlled, high-isolation AC/DC driving capability. Fig. 4 shows a schematic diagram of a circuit using theRedRock® TMR sensor RR122 to control a CotoMOSTM CS134 when driving a light bulb from a 120VAC power source. The500 ohm resistor (R1) controls the forward current flowing through the CS134 internal LED diode. When there is a magnet present to provide magnetic flux exceeding the operating point of the RR122, the CS134 relay will turn ON and AC current will flow through the light bulb to illuminate it. By using a combination of a RedRock® TMR sensor and a CotoMOSTM MOSFET relay, a compact solution to drive a load from an AC power source is achieved – creating an idea solution for many IoT applications.
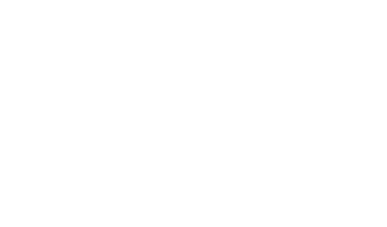
For more information including how Coto Technology’s application support can help with your design efforts, please contact redrock@cotorelay.com or visit www.cotorelay.com