How To Pair A Magnetic Sensor With The Right Magnet For A Cost-Effective Solution
Due to their inherent “contactless-ness”, small size, low cost and high reliability, solid-state magnetic sensors have become the preferred solution for many products and applications over the last few years. These same features also make them an attractive alternative to other technologies such as electromechanical reed switches. Unfortunately, many purchasers within the solid state magnetic sensor market use the cost of the sensor, itself, as the predominant factor in the component selection.
Instead, it is important to keep in mind that in any magnetic sensing solution, there are two equally important considerations: a magnet to produce a magnetic field and a sensor that can best detect it.
At first glance, it may seem easy to choose parts that will work well together and meet cost requirements. However, that chosen combination might not be the optimal one. By taking the time to fully understand the environment in which the sensor and magnet will need to operate and determine which specifications will make the ideal combination, one can achieve additional benefits, such as a reduction in cost and product size as well as addressing possible supplier concerns.
For example, one common way to reduce magnet cost is to switch to a sensor with a higher magnetic sensitivity (i.e., a sensor that activates with a lower magnetic flux density). If the sensor is “less demanding” in terms of the field it needs to work with, the magnet can be swapped out for one that produces a lower field. And, because magnet cost depends greatly upon its physical volume, magnetic strength and the material composition, choosing a smaller or weaker grade of magnet can lower cost, without sacrificing reliable activation of the sensor.
To illustrate this, consider an application where a TMR (Tunneling Magnetoresistive) sensor, such as Coto Technology’s RedRock® RR122 TMR sensor series, is paired with a cylindrical magnet in the orientation shown in Figure 1. [For this example, it is assumed that there are no other magnets or ferromagnetic components nearby, other than the cylindrical magnet.] Table 1 shows the required distances at which two magnetic sensors – one which operates at 30 Gauss and the other at 9 Gauss – would be activated by different types of cylindrical magnets. Cases 1 and 2 both assume a magnet with a diameter of 8mm and a thickness of 5mm, but Case 1 assumes a Neodymium Iron Boron (NdFeB) magnet, whereas Case 2 assumes a Ceramic magnet. NdFeB is the strongest magnet grade available, but also one of the most expensive. Ceramic (also called “ferrite”) has a lower magnetic strength than NdFeB, but is also lower in cost. Case 3 assumes the same magnet material as Case 1 (NdFeB N42), but with a smaller diameter. The relative costs of all three magnets are also included in Table 1, and are based on commercially available products.
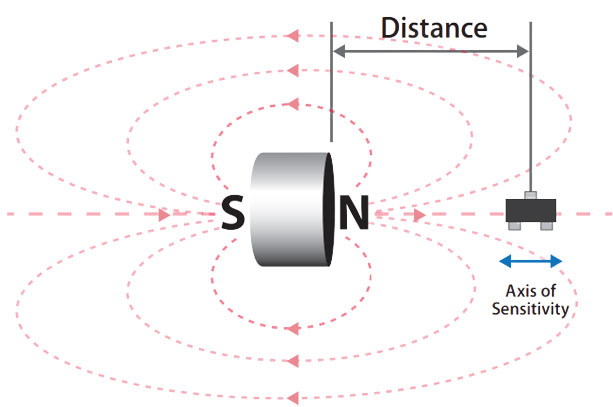
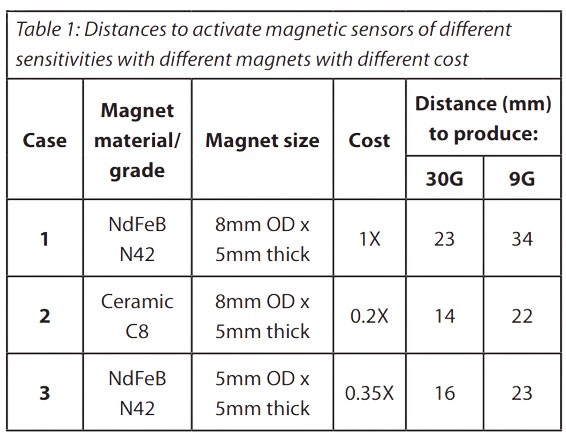
Assuming a baseline case where the magnet in Case 1 is paired with a 30 Gauss sensor, the sensor would activate when the magnet is up to 23mm away. If the sensor was swapped with one that activates with 9 Gauss, the magnet in Case 2 (Ceramic magnet), can achieve a similar distance (22mm) with only 20% of the cost of the baseline magnet. And the magnet in Case 3 (NdFeB with smaller diameter) can match the baseline distance with only 35% of the baseline magnet cost. For reference, 30-40G is a common activation threshold for Hall Effect sensors. Alternatively, RedRock® RR122 sensors, can activate with as little as 9 Gauss.
In addition to the cost benefit, switching to a ceramic magnet can also help with availability issues. Over the past few decades there have been rising concerns over both the availability and price fluctuations of rare earth magnets, such as NdFeB. While the great majority of rare earth magnets are manufactured in China, ferrite magnets are more easily accessible through worldwide manufacturing and are cheaper to manufacture.
One common way to reduce magnet cost is to switch to a sensor with a higher magnetic sensitivity.
Complex Applications can be Game-Changers
It should also be noted that there are still other issues that could come into play within more complex applications; one example might be the unanticipated presence of stray magnetic fields that might inadvertently activate the sensor when the activation magnet is out of range of the sensor. Additionally, some applications have other ferromagnetic components nearby, such as coin-cell batteries, screws, etc., which could affect the magnetic field seen by the sensor. Temperature and demagnetization performance is also different between various magnet materials. For all of these reasons, it’s always a good idea to work with a magnetic sensor supplier who has a solid understanding of magnetics and can provide valuable input on how to best implement a magnetic sensing solution into a specific product. This input can come in the form of lab testing and/or specialized magnetic simulation software. With these tools, the supplier can quickly and efficiently determine the specifications for the sensor / magnet combination that will work best within the customer’s application
Conclusion: A “Magnet-Sensor Solution” approach to building your application’s BOM can reduce the overall cost of your device significantly. By choosing a more sensitive sensor, the cost of the magnet can be reduced – and your supply chain kept more stable. If your application is more complex, work with a supplier with a firm understanding of magnetic sensors to provide you with the best, most cost effective solution.
Additional Information
Coto Technology offers a line of high sensitivity RedRock® TMR magnetic sensors that can activate with as low as 9 Gauss, while offering other benefits, such as ultra-low current consumption (< 100nA) and small size.
In conjunction with this, Coto provides thorough engineering support to customers looking to optimize a magnet and sensor pairing. To find out more about Coto’s RedRock®TMR sensors, please visit www.cotorelay.com. In addition, to speak to an Applications Engineer and learn more about how RedRock® TMR sensors can help improve your designs, please contact us at appsupport@cotorelay.com.